The external keyway cutting, linear indexing, slotting and all regular works can be done by the use of this Gear cutting attachment. Spherical Turning attachment for Lathe: The spherical turning attachment was used in center lathes for machining concave, convex and spherical surfaces. Cross-threading on a wheel nut is a problem for many car drivers. The main cause of cross-threading is overtightening of the screws on the studs during a tire change or incorrect alignment of the screws to the studs. The result is that the bolt threads shift from the center and cut into the internal threads of the bolts.
On lathe, internal and external threads are cut either with the help of a threading tool or with the help of tap and die respectively.
While cutting threads with the help of a tool, the following requirements are to be fulfilled:
a. There should be a certain relation between job revolutions and the revolutions of the lead screw to control linear movement of the tool parallel to the job when the half nut is engaged with the lead screw.
b. The tool should be ground to the proper shape or profile of the thread to be cut.
In modern engine lathe, quick change gear box is provided in which different ratios of the spindle and lead screw revolutions can be easily obtained by simply shifting the change gear lever. In ordinary engine lathe, every time one has to change the gears.
For cutting a lathe an accurate screw is necessary, that the relation between the movement of the saddle, and the revolution of work be carefully controlled. This is brought about by means of a lead screw which is driven by a train of gears as shown in a set up described in Fig.
Usually the drive is first carried to the spindle called the stud which for all purposes may be assumed to be the spindle itself as it rotates at the same speed and in the same direction, unless made to reverse by the tumbler mechanism. From the stud, the drive is conveyed to the lead screw by a train of gears.
To vary the relationship between the revolutions of the lead screw and those of the stud, the train of gears may be varied. Note that the spindle gear is never changed for cutting different pitches of thread. The stud gear (driver gear) and the lead screw gear (driven gear) are changed whenever a particular ratio is needed between the spindle and lead screw.
Here is a formula which gives the required ratio between the teeth on stud and lead screw gears.

Suppose;
p1 = Pitch in mm to be cut on the job,
p2 = Pitch on lead screw, mm.
N1 = No. of revolutions stud gear is making.
N2 = No. of revolutions lead screw is making.
The second form is generally used when multi-start threads are to be cut on the job.
Threading Using A Lathe The Mechanic Parts
While cutting internal and external threads, the following points are to be considered:

i. The tool should be set exactly at the height of the centre line of job and at 90° to the job. For setting the tool, the tool setting gauge is generally used.
ii. Tool is fed either exactly at 90° to the job axis or at an angle of 27° to 30° to the job axis. The latter method is mostly adopted because complete side of the tool is used for cutting action which gives better finish on the threads.
iii. While cutting threads, the speed of job is reduced to one third or one-fourth of the job speed used in turning operations.
Related posts:
tipusnr
Member
- Joined
- May 15, 2004
- Messages
- 1,692
- Location
- Reynoldsburg, OH, USA.
Threading Using A Lathe The Mechanic Machine

Threading Using A Lathe The Mechanic Knife
The 1/2 Hp motor is strong and once I converted the belt access door to thumbscrews changing speeds is not a real issue. The two BIG drawbacks are the fact that the tailstock backs off (no matter how tight you have it) and the toolrest is really inconvenient to adjust in and out as it uses a bolt with a nut below the bed. The LITTLE drawback is that the headstock does not have an MT2 taper (or MT1 for that matter) so everything has to screw on to the external threads.
I've been using it for a horizontal sander but now have one of those. I have two thoughts.
1. Shorten the bed and use it to rough turn bowls (I have a 4' plate and a talon chuck adapter. I can bring the live center on the tailstock all the way back to lock and use pressure to secure it. Shortening the bed would give me back some counter space as I'm not likely to turn 40' deep bowls.
2. Turn it into a permanent buffing and polishing station. The rub there is the lack of an MT2 so I would have to have a mandrel custom made. I talked to the machinist at work about grinding off the end of spur center and welding it to threaded rod to put washers and nuts on for holding the three wheels. He started to say it was a dumb idea then thought about it and changed to 'dangerously stupid idea'. At least he doesn't soft soap me! His issue was with the softness of threaded rod.
I am eager to hear what any of you have to say about either idea. Maybe you have one I haven't thought of.
I hate to throw it away and feel it would be dishonest to sell it to someone unaware of the problems.. If you're in the local area you can come and get it for $30.00 cash or check (no PayPal)[}] and come up with your own ideas.
Who knows it could be operator error but I don't think so!!!
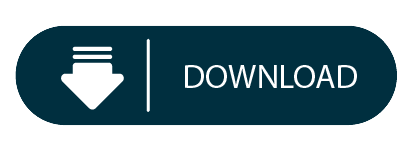